Here’s a first look at a new in-store micro-fulfillment system we designed for a global home goods retailer. It’s the company’s first in-store automation/micro-fulfillment operation in North America.
The client wanted to find a way to utilize its store space to improve its customers’ shopping experience through enhanced processing of “Click and Collect” and “Click and Deliver” offerings.
Not only did this call for a micro-fulfillment solution that would utilize only a small percentage of the client’s store footprint, it also required utilizing a non-traditional mix of storage mediums as well as a mix of robotics capable of tackling its unique inventory and fulfillment challenges.
The client’s product offerings vary greatly in size, weight, and the speed at which they sell. The diversity makes filling customer orders extremely challenging and often inefficient from a handling, storage, and picking perspective.
Traditional automation solutions favor product lines that fit one-size-fits-all storage mediums, and typically breakdown when it comes to combining more than one storage medium into a single fulfillment solution. They also favor products that sell at similar speeds to avoid the additional handling challenges of mixing fast movers with slow movers.
In offering a solution for this challenge, MSI Automate developed the industry’s first Goods-to-Person fulfillment system to support each, case, and pallet picking/replenishment in the same station. Product is supplied via totes, shelves, and pallets to the same station at the same time. This enables our client to fill orders with product ranging from fast to slow movers, small to large items, and even conveyable and non-conveyable SKUs from the same station.
The system is built around two Universal Work Stations (UWS) that are supported by a mix of autonomous robots. Operators are directed by pick/put-to-light technologies to execute fulfillment related tasks including induction, replenishment, picking, packing, and cycle counts.
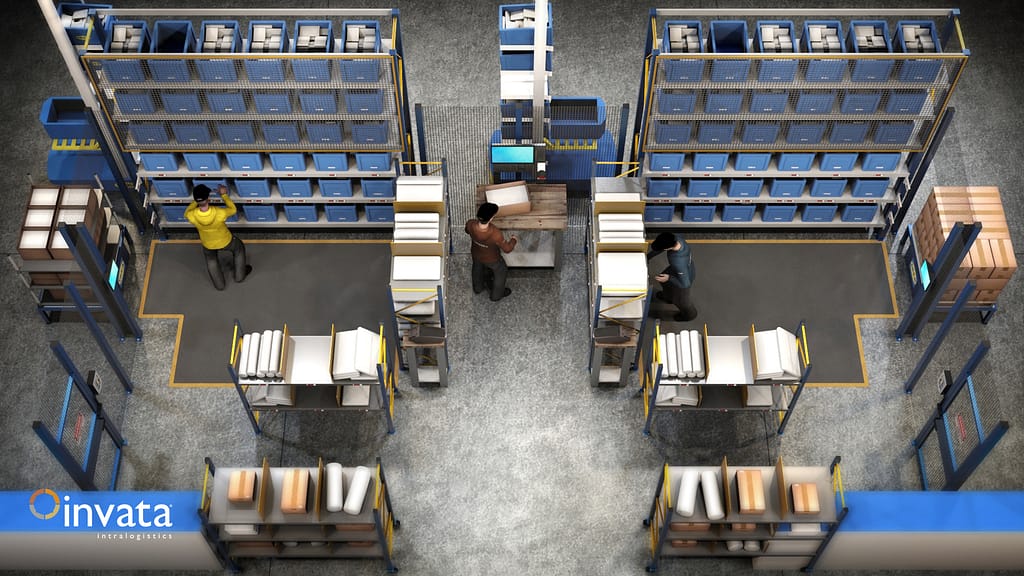
Between the two work stations is a packing station in which orders are packaged for delivery or pickup. The entire operation, including robotics management, is run by MSI Automate’s Automate Warehouse Software.
Narrow-aisle, high-density racking houses the totes, mobile shelving units, and pallet stands used to hold the company’s mix of product and are serviced by two AMR types.
System benefits include:
- Increased picking productivity for filling multi-line “Click and Collect” and “Click and Deliver” orders
- Decreased labor requirements
- Increased storage density
- Enhanced coworker morale thanks to ergonomic UWS stations.
To further enhance the efficiency of the operation, MSI Automate also developed a virtual reality training module to enable trainees to get virtual hands-on training for every task they will be asked to perform in the Universal Work Station without ever stepping foot in the station. So no production efficiency is lost to training new coworkers.
If you’re considering micro-fulfillment solutions for your company, let us know what you want to accomplish, and we’ll show you how you can.
Walter High is VP Marketing at MSI Automate, where he has worked since 2012.