Optimizing Omni-Channel Fulfillment
Overview
The MSI Automate designed, built, and controlled omni-channel fulfillment center at Destination Maternity Corporation’s 406,000 sq. ft. distribution center in Florence, NJ handles all aspects of Destination Maternity’s retail distribution, wholesale distribution, ecommerce fulfillment, and reverse logistics processing for the U.S. market and international markets.
Incorporating a high-speed shuttle ASRS, mini-load crane ASRS, a unit sorter with 600 destinations serviced by 12 induction stations, a 2000+ light directed display put wall, extensive routing and sorting conveyor systems, and wearable radio-frequency technology throughout the entire facility, the omni-channel fulfillment system and associated processing is fully controlled by MSI Automate’s warehouse execution system (WES) software, which interfaces with the host ERP and features full WMS and WCS and integrated transportation management functionality.
Processing up to 433,000 units daily, the innovative MSI Automate system has enabled Destination Maternity to realize dramatic increases in processing capacities (100% in receiving, 60% in wholesale fulfillment, 66% in retail fulfillment, 240% in ecommerce fulfillment) while enjoying a 44% decrease in workforce size and a 7.3% decrease in freight costs. Destination Maternity has also seen dramatic improvements in the areas of serviceability, visibility, flexibility, and reporting as well as throughput, processing capacity, and time to fulfillment.
Providing highly innovative solutions to complex logistics challenges, this omni-channel fulfillment center case study offers new ways of looking at systems design, automated processing, and systems software and testing.
"… a highly automated DC, built from the ground up, that simultaneously manages the complexities of the business while simplifying the fulfillment process. It’s a pretty remarkable story. "Bob Trebilcock
Executive Editor, Modern Materials Handing Magazine
Video Overview
Situation
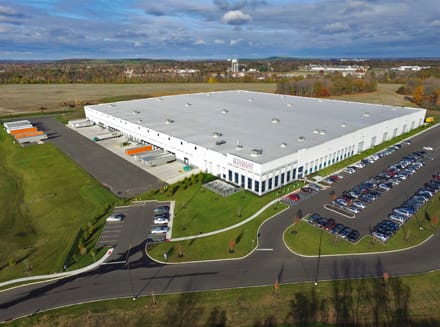
Destination Maternity’s 406,000 sq. ft. omni-channel fulfillment center in Florence, NJ.
Destination Maternity is the world’s largest designer and retailer of maternity apparel. As of January, 2016, it operates 529 retail locations under three retail nameplates: Motherhood Maternity®, A Pea in the Pod®, and Destination Maternity®, and operates 1,288 apparel departments within retailers such as Macy’s®, Sears®, Buy Buy Baby®, Boscov’s®, and Century 21®. The Company also provided maternity apparel for Kohl’s Department Stores®. Destination Maternity’s inventory is also available for direct to consumer shipments on brand websites and other ecommerce sites.
In late 2013, Destination Maternity was operating a very linear, traditional pick and pack operation in its Philadelphia-based distribution center and serviced its wholesale business operation at a separate site.
Limited by facility reconfiguration restrictions, disparate and unsupportable WCS sub-systems, processing and shipping inefficiencies, and highly labor intensive fulfillment processes in which product was handled multiple times including during receiving, put away, replenishment, and picking, the system was deemed outmoded and unable to support the company’s future growth needs in terms of customer service, omni-channel fulfillment, and order turn around time.
As a result, Destination Maternity decided to build an omni-channel fulfillment center to handle the company’s retail and wholesale distribution, ecommerce fulfillment, and reverse logistics processing.
Opportunity
Destination Maternity needed to find a system or systems that could handle all aspects of the company’s omni-channel processing requirements for its U.S. market and various international markets. These included finding ways to:
- Combine retail, wholesale, ecommerce, and reverse logics processing into one operation.
- Accommodate unique handling requirements between and within distribution channels.
- Accommodate unique packaging and delivery requirements between and within distribution channels.
- Accommodate each-handling, including receiving, picking, and shipping on all outbound orders.
- Accommodate shipping to domestic and international markets.
- Accommodate supplier compliance issues regarding the positioning or inclusion of barcodes on clothing items.
- Accommodate a single inventory stream for all channels.
- Offer flexibility in processing capabilities.
- Improve reporting and productivity tracking at the end user level.
Given the diversity of operations required in an omni-channel environment, Destination Maternity was also interested in finding ways to multi-task material handling equipment, so that its unique reverse logistics process could be managed via the same equipment that handled its fulfillment and distribution processes.
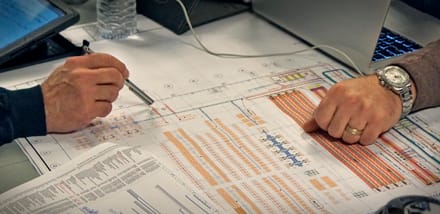
The MSI Automate team reviews system design and schedule.
The Evaluation Process
After performing a detailed analysis of its company’s production activities, the Destination Maternity Distribution team sent out a distribution analysis along with projected growth requirements to material handling equipment suppliers and WMS and WCS software suppliers with a request for concept ideas pertaining to each suppliers area of expertise.
What the team got back was a mix of disparate, traditional ideas involving a WMS which controlled inventory and order allocation, a WCS which controlled the MHE system, a wide variety of material handling equipment configurations (depending upon the supplier), and an integrator who would attempt to tie them all together.
This caused Carl Marcinkowski, Sr. Vice President of Distribution and Transportation for Destination Maternity to wonder who would take responsibility for problems they might run into upon start-up. “I had been through start-ups before,” Marcinkowski noted, “and the answers I got in response to performance issues were generally the same: ‘It’s an equipment issue,’ or ‘It’s a software issue.’ Nobody wanted to take responsibility for it all. And pretty soon, it was nobody’s issue but ours.”
That’s when Marcinkowski and his project team began evaluating non-traditional solutions.
“We had considered the traditional WMS-driven model, but we would have had to do so many customizations to a WMS to make it work the way we wanted, it would have been cost prohibitive,” noted Marcinkowski. “And then, we still wouldn’t have used a large chunk of what we were paying for.”
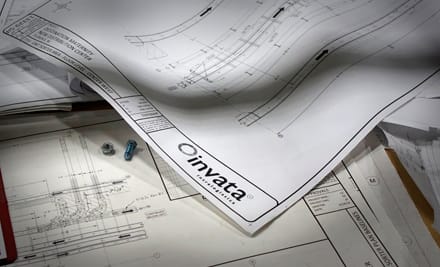
MSI Automate was founded on the idea of bringing all disciplines needed to provide and fully support game-changing warehouse automation under one roof.
MSI Automate proposed an innovative solution in which MSI Automate took responsibility for all aspects of system design, implementation, integration, and support. And beyond that, MSI Automate proposed to use its own warehouse execution software to not only control the entire fulfillment process, but to also enable Destination Maternity to multi-task the automation equipment in the way they needed to service multiple business needs.
Destination Maternity saw value in the proposal. “We had done our due diligence,” said Marcinkowski. “We had visited some 30 fulfillment operations only to find that none of them quite achieved a complete solution to our needs. We had researched a variety of designs that each satisfied different requirements, but neither met our present requirements nor were flexible enough to meet our future needs.”
“No one had come back to us and said this is how it all works, and works together — except MSI Automate. MSI Automate’s solution blended together a system that satisfied all our requirements. It was an end to end solution that incorporated all aspects of system design, implementation , integration, and support — and MSI Automate proposed to use its own warehouse execution software to control the entire fulfillment process. They also proposed to multi-task the material handling equipment to enable us to service multiple channels on the same equipment, including reverse logistics, which would enable us to get maximize return from our capital spend. We needed a complete solution from a single, fully accountable source, and MSI Automate provided that,” said Marcinkowski.
After careful consideration, the Destination Maternity team chose to work closely with a relative newcomer to the intralogistics market and selected MSI Automate to provide its new omni-channel fulfillment center.
The Solution
MSI Automate’s approach to the design of the Destination Maternity omni-channel fulfillment center was born out of a highly collaborative relationship with the Destination Maternity Distribution Team in which the two companies worked together in determining the best approach to solving Destination Maternity’s logistics challenges.
“The feedback, analysis, and insights we received from the team at Destination Maternity enabled us to take an innovative approach to problem solving that simply would not have been possible without their vision, input, and collaboration,” said Ryan Sheehan, MSI Automate CEO.
The resulting solution is a highly innovative, flexible, and adaptable one that addresses a variety of complex logistics challenges in ways the industry has not seen before:
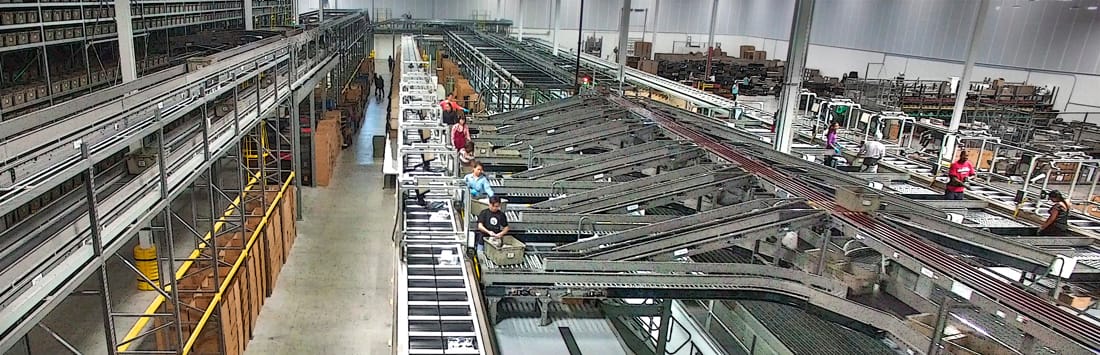
Single SKU totes from the shuttle ASRS (left side of image) are delivered via elevated conveyor to sorter induction stations as needed for order fulfillment purposes at Destination Maternity’s omni-channel fulfillment center.
A Comprehensive Approach with Total WES Control
The MSI Automate system is a complete solution, designed by MSI Automate, controlled by MSI Automate Warehouse Execution Software, and supported by MSI Automate.
There’s no third party WMS or WCS, just MSI Automate’s own WES with warehouse management, warehouse control, and transportation management functionality fully integrated into one comprehensive continuous execution system.
The MSI Automate WES communicates with the Destination Maternity ERP through an interface database that facilitates the exchange of data between the host ERP and MSI Automate’s WES production database. The MSI Automate WES then handles all aspects of receiving, put away, storage, picking, routing, order management and fulfillment, sorting, packing, labeling, and shipping for all Destination Maternity fulfillment channels.
The material handling portion of the system is also completely controlled by MSI Automate’s WES down to the PLC and device level. This includes:
- A high-speed shuttle automated storage and retrieval system (ASRS) with 2 aisles of 21 levels of tote storage (approximately 25,000 totes) and 24 high-speed shuttles which are transferred between levels as needed. Each aisle has 4 tote lifts (2 inbound, 2 outbound) and one shuttle lift. The lifts are redundant so all inventory is accessible in the event of service requirements. Each shuttle has a load handling device capable of carrying two totes and storing them two deep on either side of the aisle.
- A mini-load crane ASRS with 4 cranes in high density, high-rise bays with a combined capacity of 75,000 containers. Each crane has a load handling device capable of carrying two totes/cartons and storing them two deep on either side of the aisle.
- A bomb bay sorter with 12 induction stations, feeding 600 discharge destinations at sortation speeds averaging 15,000 units per hour.
- A multi-purpose put wall with over 2,000 light displays.
- A substantial conveyor system including, numerous 24v routing sorters, 5 narrow belt sorters, 11 merges, and machine interface stations.
- Wearable radio-frequency technology throughout the entire facility for all user transactions.
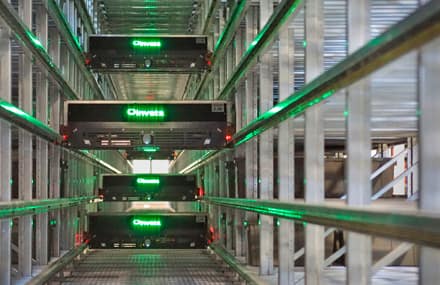
ASRS shuttles manage single SKU totes for order fulfillment.
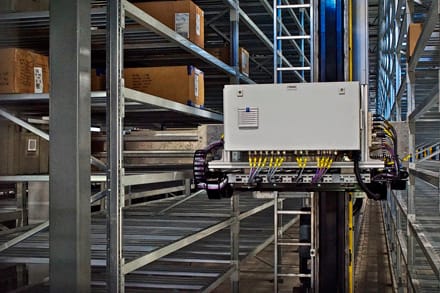
Mini-load cranes are used for high density storage of cartons and totes.
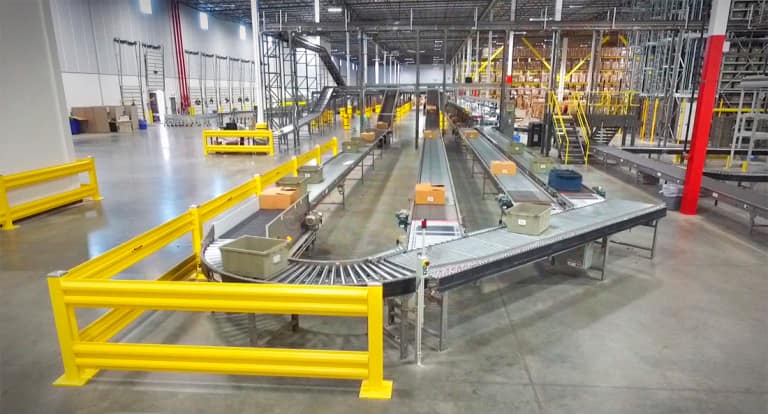
Decanting area for omni-channel fulfillment center.
The MSI Automate WES also handles the Destination Maternity reverse logistics process, which entails seasonal call backs, transfers, consolidations, repositioning, and returns for the company’s various channels as well.
“The industry has wondered whether you can run a highly automated facility without a traditional WMS. Destination Maternity’s answer is ‘Yes.’”Bob Trebilcock
Executive Editor, Modern Materials Handing Magazine
True Omni-Channel Fulfillment through Multi-Tasking Equipment
The MSI Automate system handles all aspects of Destination Maternity’s retail distribution requirements (for both lease and company owned operations), wholesale distribution requirements, ecommerce fulfillment requirements (including orders from various Destination Maternity websites as well as some of its retail partners’ websites), and reverse logistics processing requirements for its U.S. market and international markets.
In doing so, the system takes a multi-purpose approach to the use of the ASRS equipment, unit sorter, and put wall. While some suppliers had suggested Destination Maternity build a second MHE system to handle the company’s unique reverse logistics requirements, the MSI Automate system uses its WES to incorporate a different processing methodology on the same equipment used for order fulfillment.
Enhanced Shipping Efficiencies
Due to the disparate operating systems and processes used in their previous distribution facility, Destination Maternity was forced to split orders both by fulfillment process (GOH and pick-to-light) and across internal company divisions. In doing so, it was also forced to split shipments along the same lines as the orders were processed. This translated to an inability to realize shipping efficiencies that might have been possible through combined shipping.
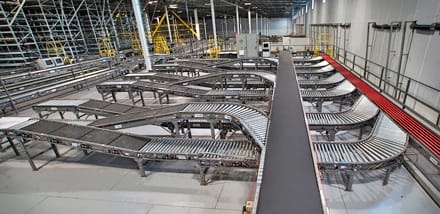
Retail, wholesale, and ecommerce orders on route to shipping area.
Thanks to the omni-channel design of the new system, inventory is now handled as a single inventory stream, multi-channel processing is handled through a single system, and, as a result, shipments can now be combined into the most efficient single method possible. This has not only resulted in a freight savings of over 5% annually, but has greatly improved customer satisfaction.
Highly Innovative System Design
According to MSI Automate CEO Ryan Sheehan, in designing the system at Destination Maternity, the MSI Automate team threw out all preconceptions they had about fulfillment system design and started from scratch.
Their goal in designing the system was to completely rethink the design process to find new and innovative ways to eliminate inventory touches, increase order accuracy, enhance productivity, and decrease toilsome labor demand.
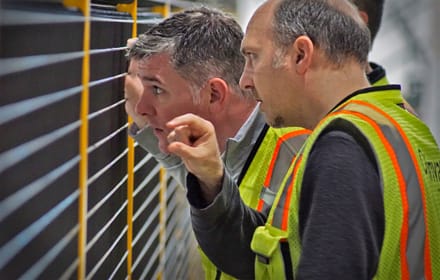
The MSI Automate team inspects shuttle ASRS performance.
Traditional solutions for retail distributors entail systems dependent on labor intensive batch picking operations as a precursor to sorter induction. In such systems, inventory is manually batch picked into multi-SKU totes (usually in waves) and then sent to the sorter for scanning and induction. It is a labor intensive, error prone process that often requires dozens, if not hundreds, of people to pick enough product to keep pace with the sorter and additional labor for returning residual SKUs to stock that are not needed on the wave. And more often than not, it results in the inability to close out waves because of errors in the manual picking process. This leads to downtime and production inefficiency. As a process that entails two labor intensive touches (picking on the front end, and scanning at induction), it is both costly and time consuming.
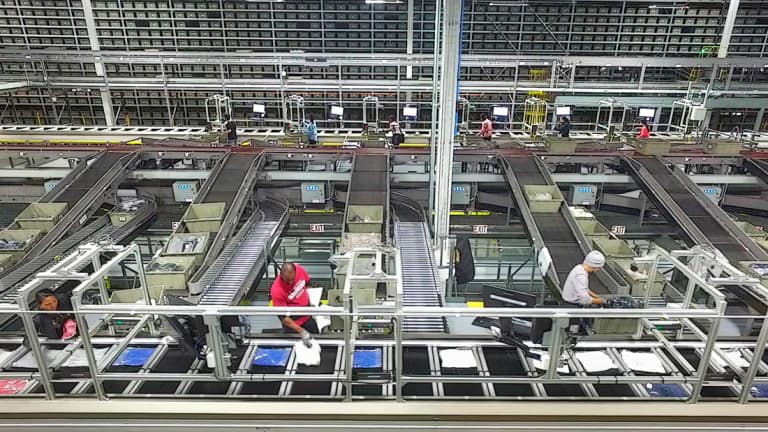
12 induction stations feed 600 discharge destinations at sortation speeds averaging 15,000 units per hour.
Instead of following suit with traditional designs at Destination Maternity, the MSI Automate team took the radical step of eliminating the manual picking process and associated batching altogether and replaced it with an automated solution in which single SKU totes are automatically delivered directly to induction as required for order fulfillment. These single SKU totes are housed in the ASRS and are called as needed for order fulfillment by the WES.
Once the totes arrive at induction, the system also eliminates the need to scan individual item barcodes prior to induction, thus solving another major challenge Destination Maternity faced due to irregular supplier compliance in the printing and placement of barcodes on inventory items. (Given some barcodes would be buried within an apparel item inside a plastic bag, or not be present at all, this posed a potential major slowdown in productivity for Destination Maternity, had it not been resolved.) Here’s how MSI Automate solved the issue:
In that only single SKU totes are sent to induction, a one-time scan of the tote LPN (e.g. the license plate number barcode which associates that tote with the SKU inside the tote) informs the WES of the item being inducted. The WES then informs the inductor of the quantity of items to be placed on the sorter via a terminal display.
As inventory items are placed on the sorter, pixelated pattern detection cameras are used to verify item placement on sorter trays within the induction station. As item placement is verified, the WES counts down the number of items remaining until no more are required. This not only allows for the elimination of individual item scanning and counting, but also enables the inductor to place articles on the sorter as quickly as they can be physically handled.
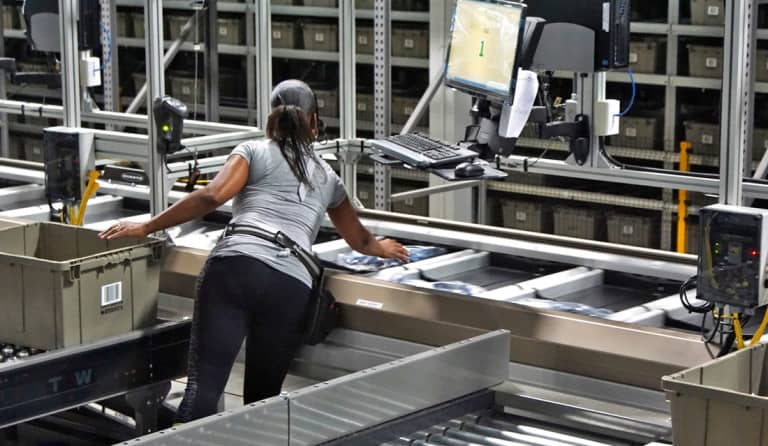
Induction terminal counts down the final item required as items are placed on sorter.
By rethinking what had become a standard operating concept, MSI Automate was able to replace two very labor intensive touches with a single high-speed touch, while raising the level of order fulfillment accuracy to near perfect. In the process, MSI Automate was also able to virtually eliminate wave processing.
Optimized Fulfillment
Traditional distribution systems utilize wave processing to fulfill a fixed number of orders before moving onto the next wave. Productivity within such systems generally emulates a sine wave with strong peaks during the initial fulfillment process and deep valleys while system productivity slows for a few remaining unfulfilled orders to be completed before transitioning to a new wave of orders.
Knowing that traditional wave processing would not suffice for the competing demands of omni-channel fulfillment center at Destination Maternity, MSI Automate developed an order fulfillment methodology in which orders are continuously fulfilled as processing resources become available.
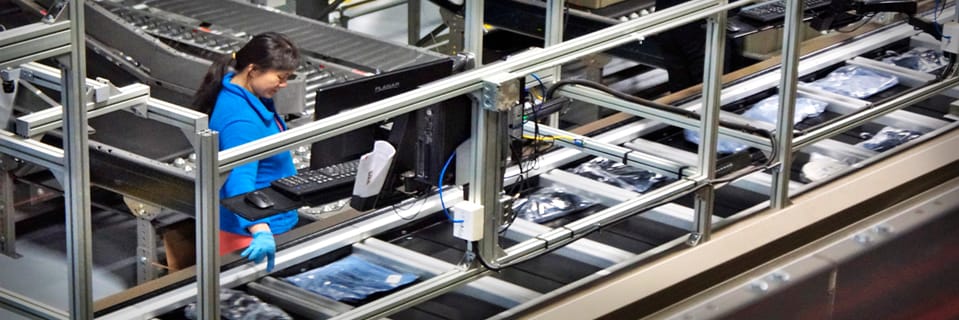
Sorter induction station at Destination Maternity.
Optimized Fulfillment involves the constant, opportunistic comparison of real-time operational conditions to the fulfillment requirements of open orders such that operational productivity can be maximized, while orders are fulfilled in the most efficient manner possible.
This dynamic optimization of process requires continuous systems analysis and algorithmic adjustment of the system order profile on a real-time basis — and often incorporates both the dynamic deployment of in-motion inventory as well as the dynamic utilization of available equipment and labor.
Here’s how it works at Destination Maternity:
Destination Maternity designates key processing criteria (set on an aggregate level) for its various customer types and associated order profiles (retail, wholesale, international, and ecommerce). These criteria pertain to transportation management matters like customer location and associated truck departure schedules, and handling procedures such as the types of packing slips, packaging, and enclosure information required for each distribution channel.
As the Destination Maternity ERP transmits orders to the MSI Automate system, the MSI Automate WES fulfills orders from the order pool using an algorithmic prioritization that is based on an evaluation of both static and dynamic real-time considerations. Some of the factors taken into consideration are detailed in the table below:
Static Considerations | Dynamic Considerations |
Customer type (Retail, test Ecommerce, Wholesale, International) | Availability of equipment resources |
Customer location
SKUs being ordered Truck departure schedule for associated location |
Availability of labor resources
SKU inventory in-motion SKU inventory soon to be in-motion |
Handling definitions | Time of day as it relates to truck departures |
In this manner the WES is constantly assessing operational conditions for the most efficient order fulfillment method given the conditions. If, for example, it is early morning and truck departure times are not weighing heavily in the algorithmic evaluation of an order, the WES may concentrate on maximizing the available in-motion inventory and search the order pool for other orders requiring those SKUs. If, on the other hand, truck cut off times are approaching, the WES will focus on fulfilling any outstanding orders with impending departures. It is a dynamic equation in which MSI Automate’s WES continuously assigns and allocates the next best variable in order to optimize the fulfillment process.
Continuous Execution
Advanced computing like the kind seen in MSI Automate’s Optimized Fulfillment methodology puts great demands on system software. But that is only the tip of the iceberg, because order fulfillment covers only a portion of the processing demands required of a true Warehouse Execution System in an omni-channel operation like that at Destination Maternity.
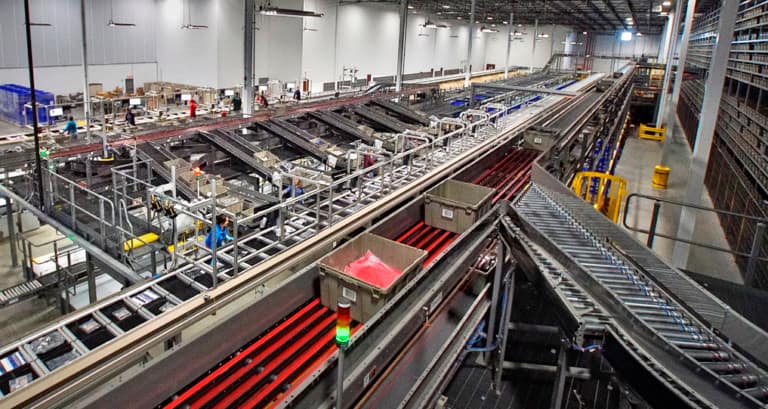
The MSI Automate system handles all aspects of Destination Maternity’s retail, wholesale, ecommerce, and reverse logistics processing.
In processing up to 433,000 units per day Destination Maternity runs a wide mix of simultaneous processes that all put demands on the WES software controlling the system.
These include receiving, transfers, customer returns, put away, allocation, decanting, replenishment, picking, routing, sorting, bagging, packing, shipping, and more.
The complexities in the MSI Automate WES receiving process alone range from communications with the host ERP for assigning and confirming ASNs and unplanned receipts, to an extensive inventory inspection process and the possible ticketing of individual apparel. It can involve the splitting or consolidation of cases, the generation of carton labels and pallet sheets, and an array of handheld scanner transactions all competing for interaction with the same database and systems software that is simultaneously handling all the queries, transactions, and procedures for the entire operation.
Real-time operational assessment and adjustments for the omni-channel operations that take place at Destination Maternity required the design of a WES capable of simultaneous and continuous execution of processes across all channels. To achieve continuous execution, the MSI Automate team had to ensure millisecond (or better) computing capabilities for database queries and transactions, systems decisions, and procedures execution for many of the processes required of the WES.
That is why, in designing the Warehouse Execution System for Destination Maternity, the MSI Automate team focused its energies on one governing principle:
Make Every Millisecond Count®
On a developmental level this translated to the critical design strategies of managing database concurrency, writing lean, purpose-driven code, creating elegant algorithms, and constantly fighting for innovative ways to maximize the efficiencies of the continuous execution process that is required for a WES responsible for omni-channel system performance.
Simulating Reality to Prove Out Performance
The deployment of the omni-channel fulfillment center at Destination Maternity involved the integration of ASRS and sorter technology that MSI Automate had never employed in one of its automated systems before.
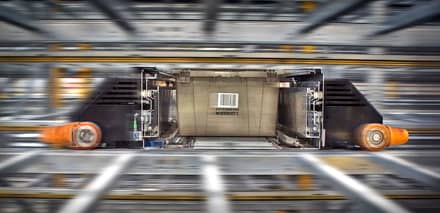
An MSI Automate high-speed shuttle moving totes within an automated storage and retrieval system.
In integrating the technology into the system, MSI Automate not only developed new electrical engineering, controls, and automation software for the equipment, but also developed a fully functioning simulation environment in which to test and prove out the automation software applications (used to operate and control the equipment) prior to going on site.
In fact, MSI Automate used simulation technology to test and verify the performance of the system software for the shuttle ASRS, the mini-load crane ASRS, the bomb bay sorter, and the put wall displays. In doing so, it was able to:
- Execute and test the core logic component (business rules) for each application.
- Evaluate interactions between the equipment and the system software and examine the resulting behavior.
- Test system messages and recovery in response to select component failures within the system.
- Hone communications between the equipment, PLCs, and software.
- Optimize associated database performance.
- Validate system performance before installing the system.
In taking the highly innovative step of creating simulation environments for the Destination Maternity system, MSI Automate was not only able to ensure its applications and associated equipment would perform as expected once in the field, it was also able to provide assurance that future process changes could be tested and confirmed with minimal interruption to production.
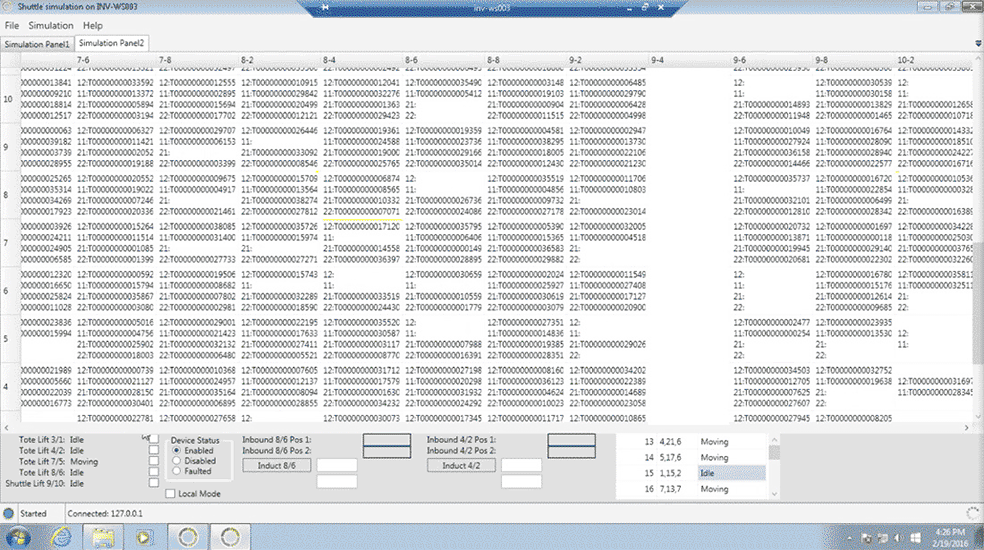
But, most importantly, MSI Automate’s simulation testing enabled a seamless system start-up, which proved critical to a changing distribution strategy that was taking place at Destination Maternity at the same time the MSI Automate system was scheduled to go online.
A True Test of Technology and Proof of Concept
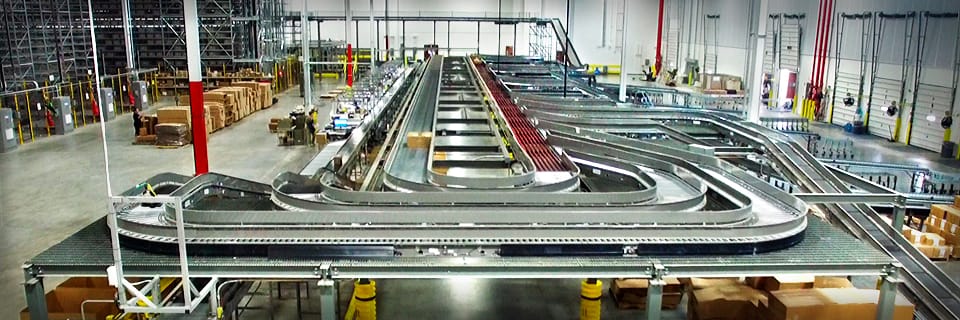
The shipping mezzanine for Destination Maternity's Omni-channel distribution center.
In the months leading up to the system start-up of its new omni-channel fulfillment center, big changes were taking place at Destination Maternity. A new CEO had been hired who was changing the way the company did business.
On a strategic level, the new CEO’s vision involved transforming the way Destination Maternity would plan, distribute, display, and promote its inventory. It also involved moving the company from a pull-based allocation approach to a specialty retail push model and reclassifying perception of company inventory from fungible to perishable.
At the fulfillment level this meant that everything from the calendarization of the business to the lifecycle of the product was in flux. Buying patterns, receipts handling, transfers and consolidations, outbound shipments, the cadence of the business, was all being reviewed, changed, and improved upon.
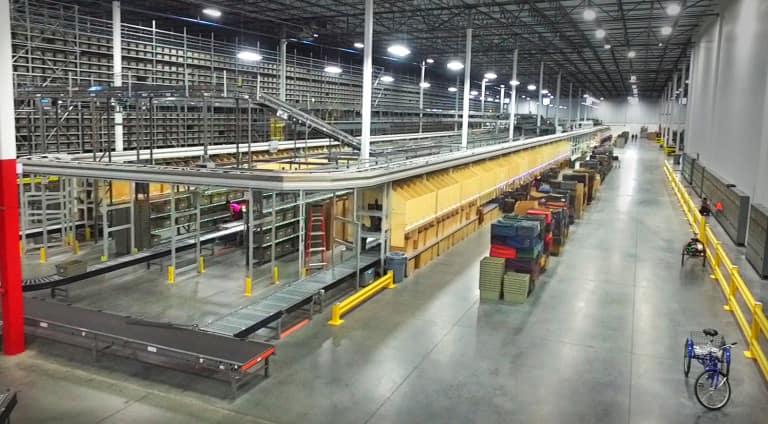
Elevated bomb bay sorter flanked by one of two automated storage and retrieval systems that service it. Sorter services 600 discharge locations.
For Carl Marcinkowski, that meant having to change the way his operation did business at the same time he was shutting down one facility and starting up another.
It was too late to make changes to the new fulfillment center design, so the system start-up would be a true test of the flexibility MSI Automate had promised with the new system.
The test came two weeks into start-up. Two million pieces of product had just been transferred into the new facility when Destination Maternity was hit with some of the heaviest days of inbound receipts (and subsequently, outbound shipments) in the company’s history.
Marcinkowski knew the surge was coming. What he didn’t know was how well his new system would handle it.
It was a new system that incorporated a vast array of advanced technology with dozens of sub-systems that all had to communicate, interact, and execute with precision to achieve the required throughput. And it was being run by operators who had been trained, but not yet tested at this level.
When the day was done, the system had handled it. Without a hitch. And record numbers had been achieved within the first two weeks of operation.
“It proved that we created a system with the flexibility and adaptability to bob and weave and handle big changes in the way we do business,” said Marcinkowski. “We came up really quickly. And the fact that we were able to come up so quickly — transferring over two million pieces of inventory into this building, while dealing with process changes within the company, and modifying a lot of the cadence of what we were doing — is a testament to the new system’s performance capabilities… and to the design and foresight that went into it.”
The Results
Thanks to MSI Automate, Destination Maternity went from a very linear traditional pick and pack operation that relied on disparate systems and processes, to a new single inventory stream, omni-channel fulfillment center that handles all aspects of the company’s retail and wholesale distribution, ecommerce fulfillment, and reverse logistics processing for the U.S. market and international markets.
In doing so, Destination Maternity has realized a 44% reduction in workforce, while realizing a freight savings of 7.3% annually as compared with their previous operation.
The new MSI Automate system provides Destination Maternity with the ability to fulfill orders based on each channel’s unique handling, packaging, and delivery requirements (including variations within channels). And it has enabled the company to work around barcoding placement issues on certain apparel items.
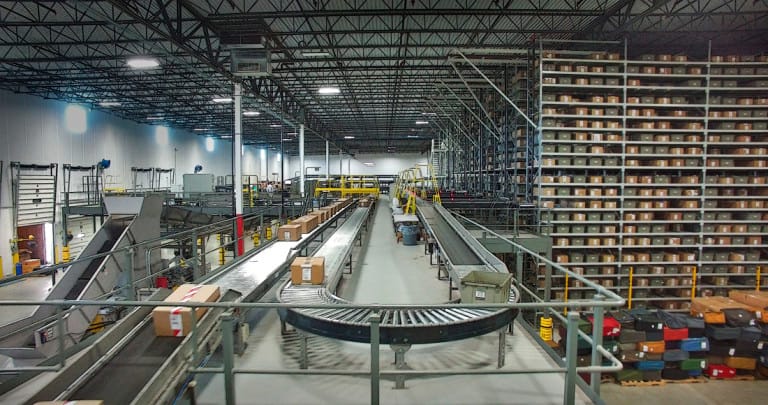
Mezzanine level primarily used for storage and retrieval from mini-load cranes and product decanting prior to sortation.
The system has also enabled Destination Maternity to utilize the same equipment to accomplish disparate tasks: A single material handling system processes the company’s distribution and fulfillment requirements as well as its reverse logistics requirements — eliminating the potential capital expenditures and operating expenses for the secondary systems recommended by competing potential system suppliers. And, in eliminating the need for a batch picking operation to feed the sorter, the MSI Automate system lowered potential labor related expenses for the operation as well.
“We’re so much more flexible now in the ways we can manipulate orders, process orders, and service our customers,” said Carl Marcinkowski, Sr. Vice President of Distribution and Transportation for Destination Maternity. “The flexibility of the system allows us to service our channels in the ways in which they need to be serviced. We have the ability to pick and choose service levels, the way we sequence our customers, and realize savings from processes like drop orders to hub induct programs.”
“The way we service our web business has improved dramatically as well,” Marcinkowski adds. “We’ve gone from taking days to service ecommerce orders, to hours— while also servicing our stores and our wholesale customers at the same time.”
The company has seen system related improvements across the board, largely due to the efficiencies of process within the new omni-channel fulfillment system:
- The receiving process has seen a 100% increase in capacity.
- The wholesale fulfillment process has seen a 60% increase in capacity.
- The retail fulfillment process has seen a 66% increase in capacity and now requires only 40 people to hit the same fulfillment rate that previously required 90 people.
- And the ecommerce fulfillment process has seen a 240% increase in capacity due to an 82% reduction in the number of touches required to process ecommerce orders — which dropped to 5 touches from 29 touches for the previous operation.
“Our visibility into orders and our internal tracking capabilities have also improved dramatically, as has our vision into operations and system performance,” Marcinkowski notes. “The MSI Automate system has enhanced the serviceability, visibility, flexibility, reporting, and, of course, productivity of our operation.”
“Our throughput, capacity, and time to fulfillment is a lot better.” Marcinkowski concludes, “while our operating, shipping, and labor related expenses are a lot less.”